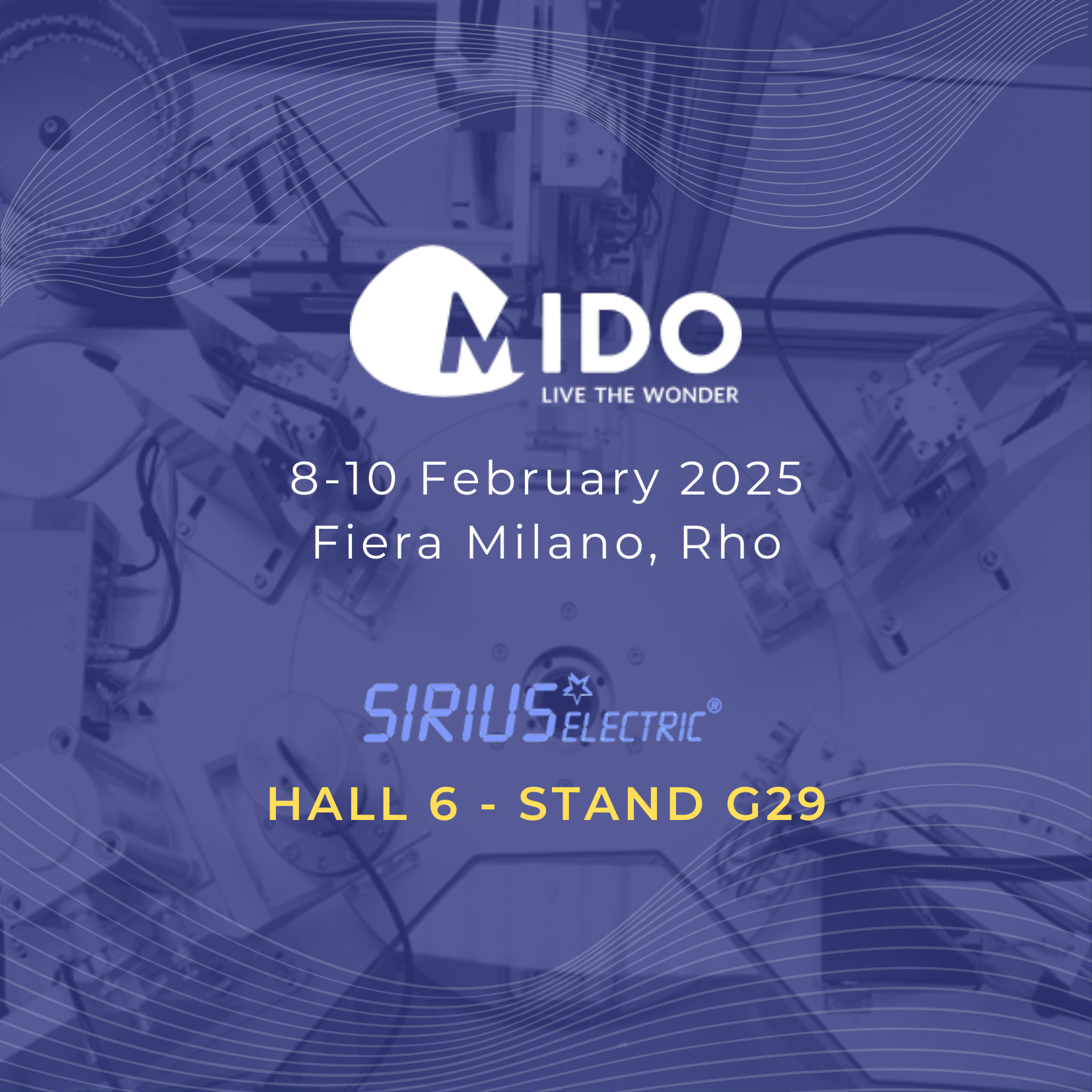
From 8 to 10 of February 2025 we will join MIDO, the leading international eyewear tradeshow.
On this occasion, we will introduce our brand-new MINI Vibration Welder we will introduce our innovative MINI Vibration Welder, crafted with cutting-edge technologies (3D CAD, CNC) and perfectly suited for compact and customized eyewear production lines.
Meet our team at Pavillion 6, Stand G29 with our welding technologies dedicated to eyewear: the special automatic vibration welder, the manual VSP vibration welder and the new MINI welding machine. All these solutions are suitable for the production of acetate glasses.
New MINI Vibration Welder, for compact and customized eyewear production lines
We are pleased to present our latest innovation, the MINI Vibration Welder, a state-of-the-art solution designed to meet customized needs of eyewear manufacturing. This compact machine is engineered with advanced technologies such as 3D CAD and CNC, and represents an ideal choice for small-scale and customized production lines.
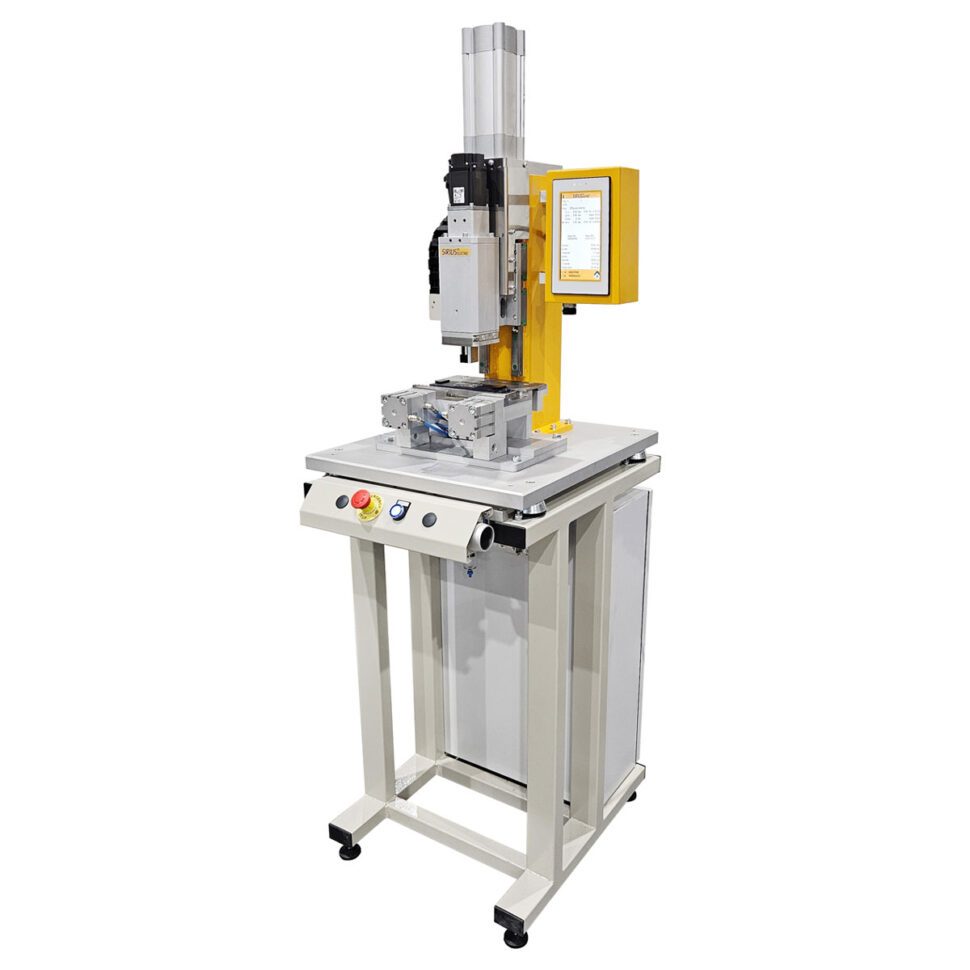
Key Features and Technical Specifications:
- Cylinder Diameter: 80 mm, ensuring precision and stability
- Optical Ruler: For accurate measurements and positioning
- Brushless Motor: Provides high efficiency and reliability
- Serrated Vibrating Head (80×80 mm): Ensures effective and uniform welding
- Proportional Valve: Enables precise control for optimal performance
- Touchscreen Display: For intuitive operation and seamless adjustments
This cutting-edge machine is specifically designed for the production of acetate eyewear, offering unparalleled precision and efficiency.
Special automatic vibration welders for eyewear
Our automatic welding machine represents a further advance in the production of acetate glasses. Three warehouses are filled with the parts to be assembled. A controlled and programmed system of electric axes carries the pieces in place that will be subsequently welded by means of circular vibration. The programming is simple and intuitive thanks to the large touch screen panel on the welding machine. The dimensions of the pieces are defined so that the software knows what is contained in the warehouses, bringing the pieces to the exact desired location. The automation is made of painted steel with components of primary choice. The welded parts immediately pass into the milling department, so that it is no more necessary to wait for the solvent reaction. The welding machine is equipped with a router for networking, with the possibility of remote assistance according to the principles of Industry 4.0.
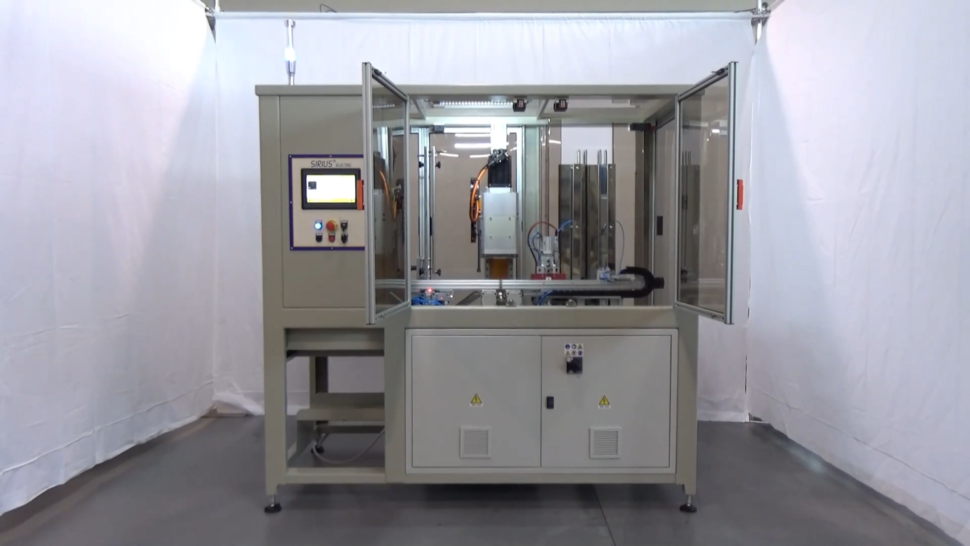
VSP 405 vibration welder
This technology is used for welding thermoplastic parts that have complex geometric shapes or when the material itself cannot be welded using traditional technologies (ultrasound – hot plate).
The vibration is circular. Unlike conventional vibration welders, vibration is obtained through the displacement of a specially shaped shaft. This is very important because it allows the client to make the necessary fixturings. The mechanical and electrical solutions available create optimal operating conditions with several adjustment possibilities, making the welder ideal for most welding applications. Management and cycle control are handled by a microprocessor system.
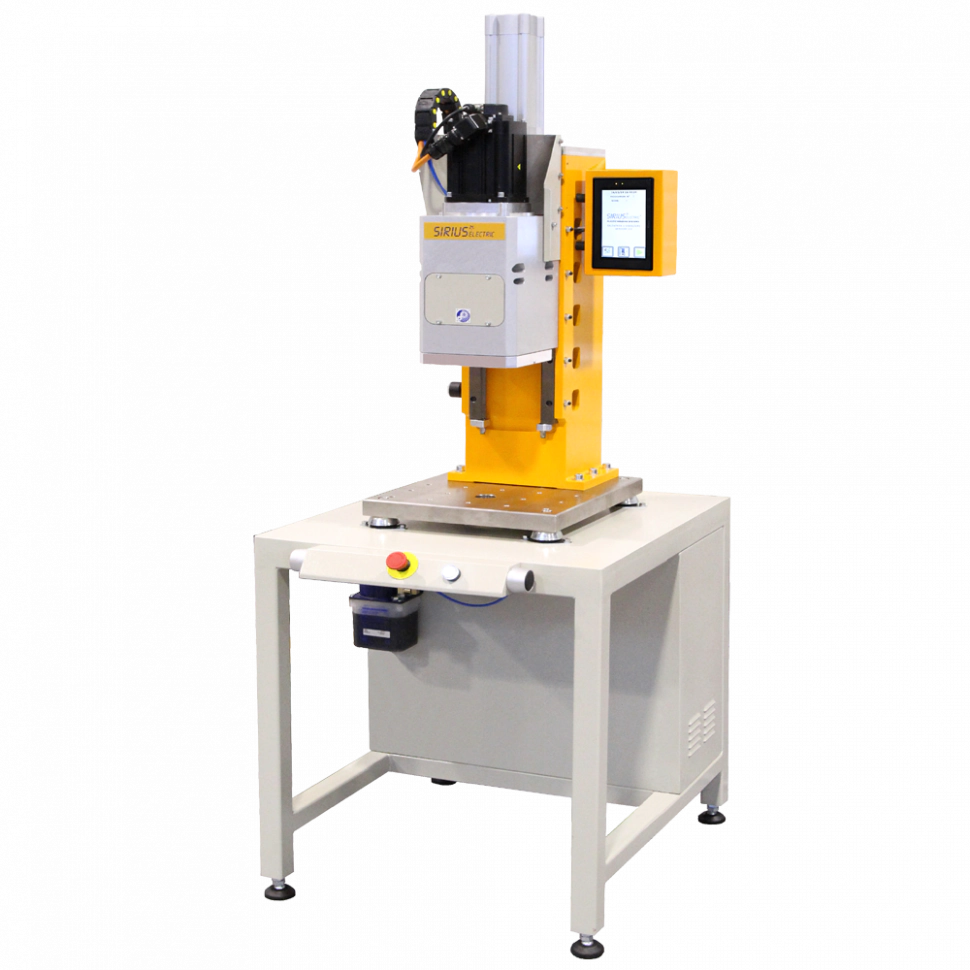